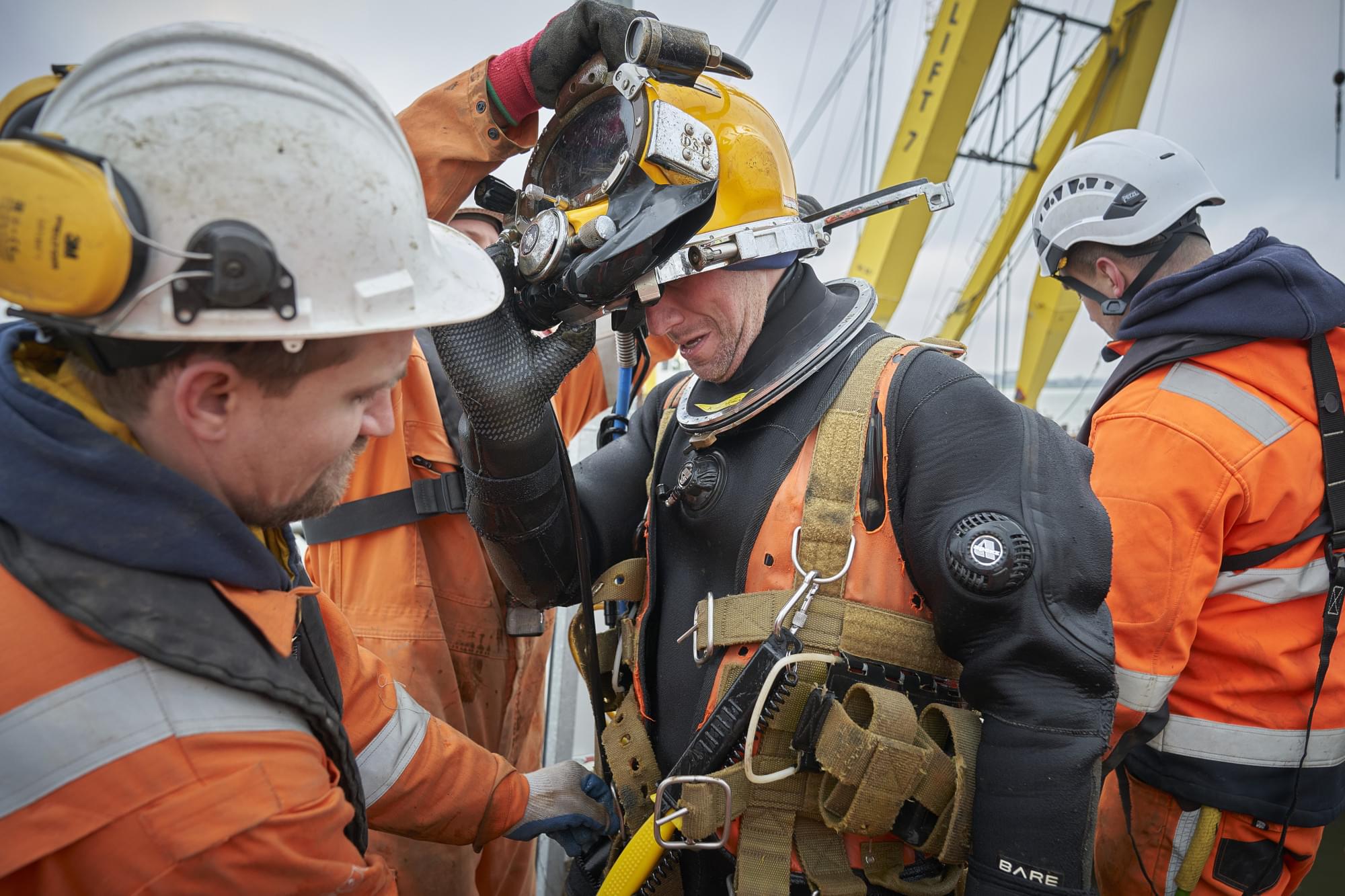
Monstrous task at great depths
Published on: 23/05/2023
Since 2018, DISA International has made a significant contribution to the A24 Blankenburg Connection project. During peak periods, the pioneer in groundbreaking underwater solutions assisted the BAAK contractor consortium with a remarkable team of 180 divers. Even now, various teams from DISA are engaged in precise cutting of the combi-wall with little to no visibility underwater.
A substantial part of the Blankenburg Connection is built (partially) underwater. In the preliminary stages, BAAK had extensive communication with DISA International to approach the underwater structures as efficiently as possible. "It is undoubtedly a monster task for us," says Didier de Graaff, Managing Director of DISA International. "During peak periods, we were active seven days a week, day and night. We also relied on our international partners for this task. Other projects and clients should not be hindered by this massive undertaking."
LETTERBOX PIT
Currently, DISA International is busy removing the trusses and burning away the combi-wall in the ramps leading to the Maasdelta immersion tunnel at a depth of 32 meters. "These so-called Letterbox pits on the north and south sides served as buffers during the construction of the ramps. They ensured watertight closure of the ramps and also acted as collision protection for the construction pit behind," says Marc Veldhuizen, supervisor at DISA International. "A letterbox pit consists of two rows of 15 pipe piles each, with diameters ranging from 1.60 to 1.85 meters. The piles are connected with sheet pile walls, and three stacked trusses are placed between the two rows. In 2018, underwater H-beams were welded to these pipe piles, serving as support points for the three trusses weighing 100 tons each. When dismantling the letter boxes, we first remove the trusses using a floating crane, after which we cut and lift the pipe piles at a depth of 32 meters." The pipe piles themselves are far from lightweight, weighing 85 tons each.
CUTTING MOULD
Cutting through the combi-wall is quite complex due to the depth, three different underwater currents, and limited visibility for the diver. "For cutting, we employ a specially developed cutting mould," explains John Penson, Operations Manager at DISA International. "In combination with a PVL precision cutter, we can precisely cut the combi-wall down to the centimeter. The PVL cutter offers much higher precision compared to a thermical lance. It also allows for faster and safer cutting." DISA International is one of the few companies proficient in this specific cutting technique. "After cutting, we place a closure cap on the outer row of pipe piles and measure the height of the pile from all four sides," adds Veldhuizen. "Based on this measurement, the exact height of the shimming plates is determined, which support the immersed element. The shimming plates serve as a corrective leveling system, ensuring that each pile has the same load-bearing capacity in relation to the element." DISA International also provides necessary assistance during the immersion of both tunnel elements of the Maasdelta tunnel. "Our divers contribute to the installation of the actual tunnel elements," says Penson. While our work is not yet fully completed, we look back on an exceptional project," concludes De Graaff. "Moreover, the project was executed with a very high safety score, which we are proud of."